A case to redesign the handlebar system of a foldable bike by use of Additive Manufacturing (3D printing) led to a design that would make use of benefits like advanced lattice geometries to create a product that are aesthetically innovative while being functionally superior to traditional manufacturing methods at the same time.
To save time, the idea was to model half the handlebar (the right side) so that it could be mirrored. A square shape was thought to be good for the central part (1) as it would make locking both horizontal parts with a steering column easier (2) by using standard nuts and bolts. In the transition to a round handle shape, a diamond-like (3) area was designed to be able to fit a brake lever and a gear shifter (4). On the outer part of the handlebar, a standard diameter was used so that existing rubber grips could be applied if wanted (5). The steering column’s main design feature was to include half of the hinge from an existing foldable bike so assembly with that bike could be achieved easily.
In collaboration with Aime Vesmes, Yodit Kinfe, Sai Bharath Kolisetty, Sandra Säfdal and Philip Lees.
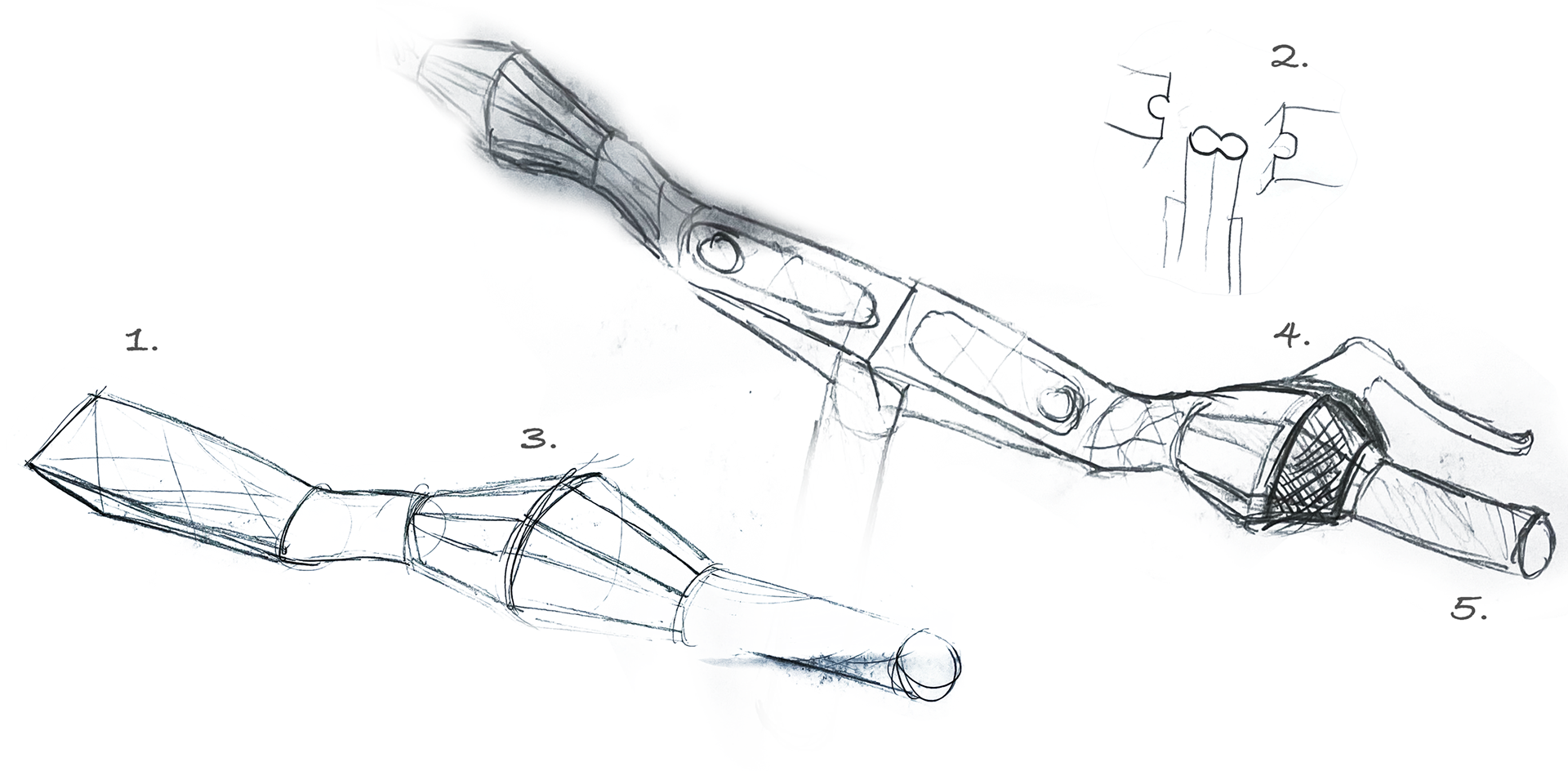
Sketch of the handlebar concept with its square centre and various features.
After the general shape of the parts was done in Fusion 360, nTopology was used which is a software that is based on implicit modelling technology which gives way to create advanced geometry with less computational power through the use of field-driven design. The hinge, was designed by taking measurements and photographs of the hinge on the reference bike’s steering column.
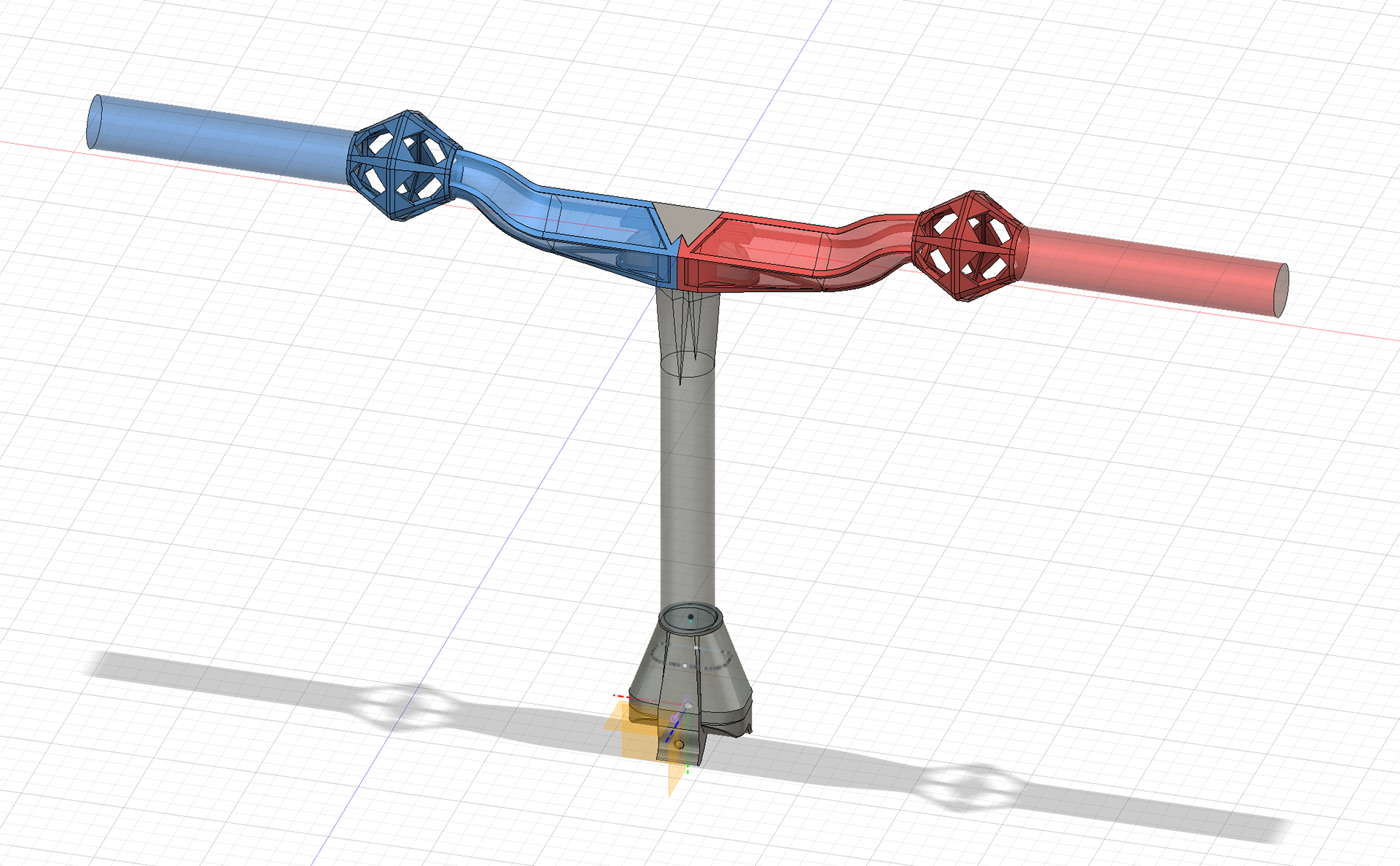
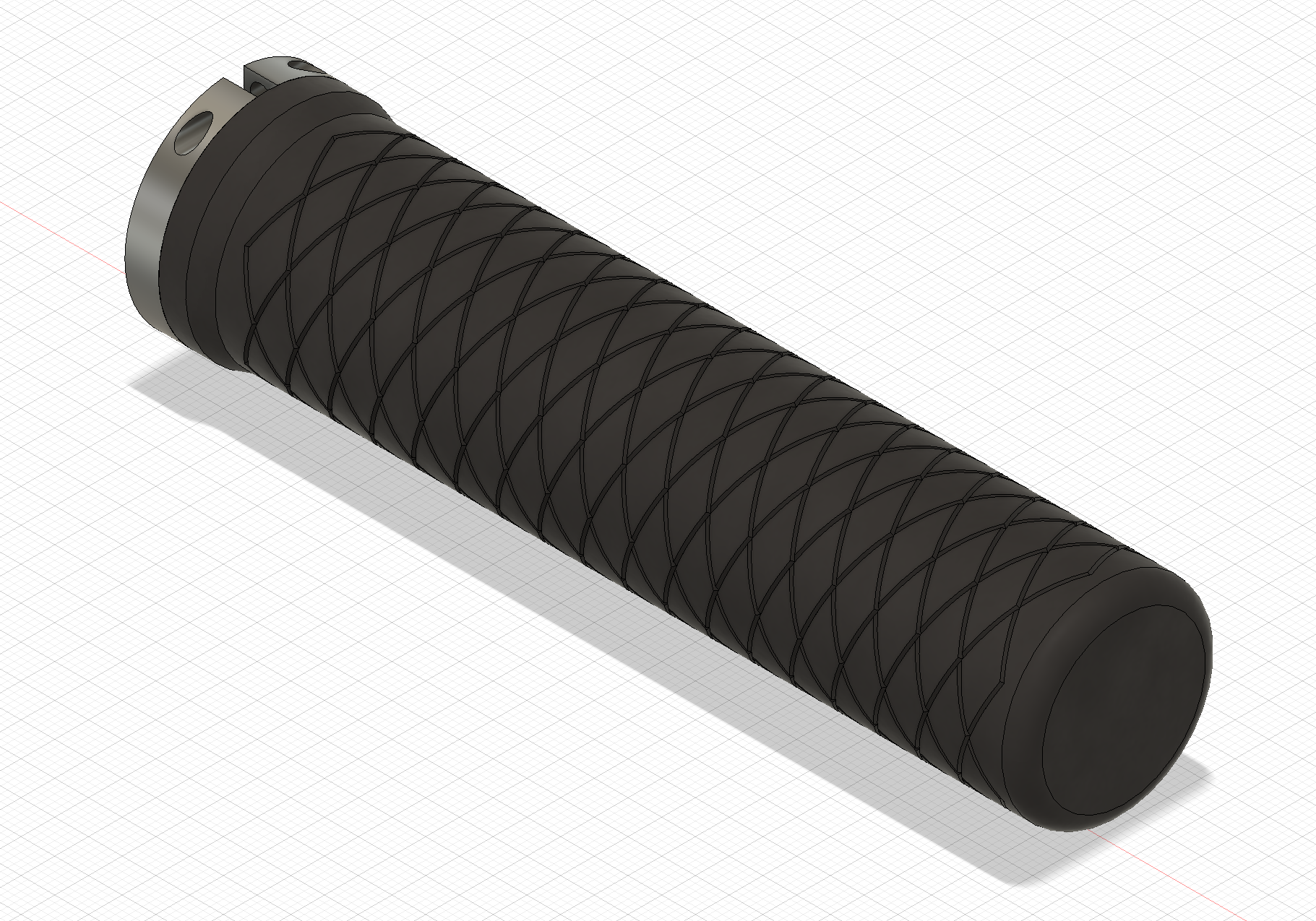
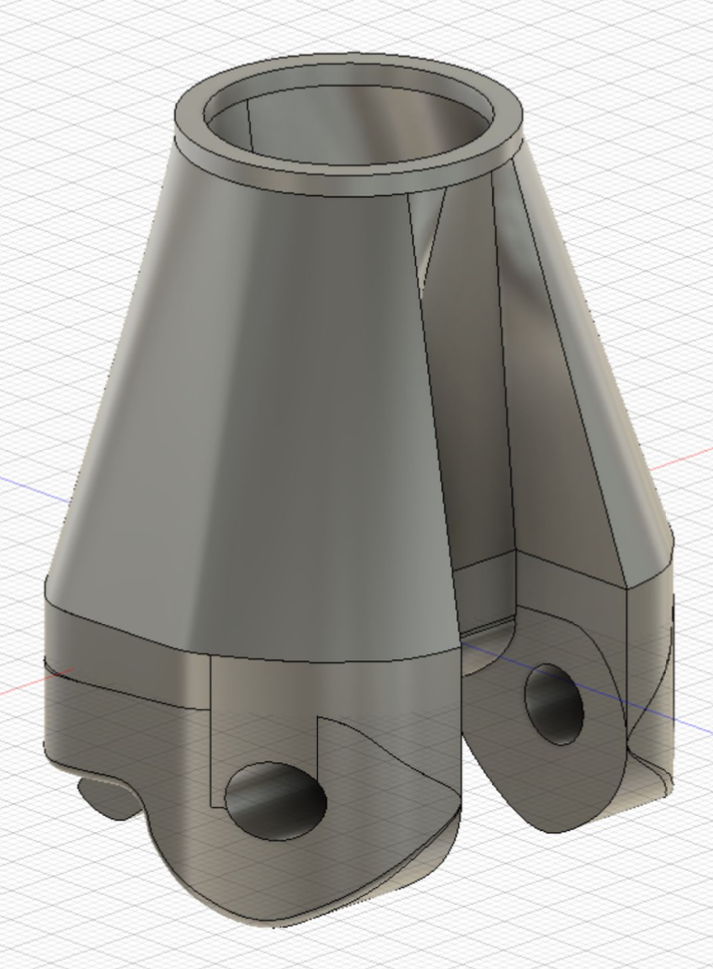
Full assembly in Fusion 360 (left) with rubber grip (middle), and hinge part (right).
Considering Design for AM when using nTopology, an organic voronoi lattice structure was created with varying size to reduce weight and make cabling for brakes and shifters possible within the parts. When comparing the lattice structure design with regular solid walls, the weight of the parts could be reduced by 50% which amounts to a total weight of around 1 280 g for the whole handlebar system. Additionally, the handle part was designed with small holes that made the surface rougher to give the user, or the added rubber handles, a good grip. The maximum hole size was set to around 8 mm and deemed not to require support for printing with LB-PBF. As a starting point for finite element analysis and polymer printing, an average feature thickness of 2.5mm was set.
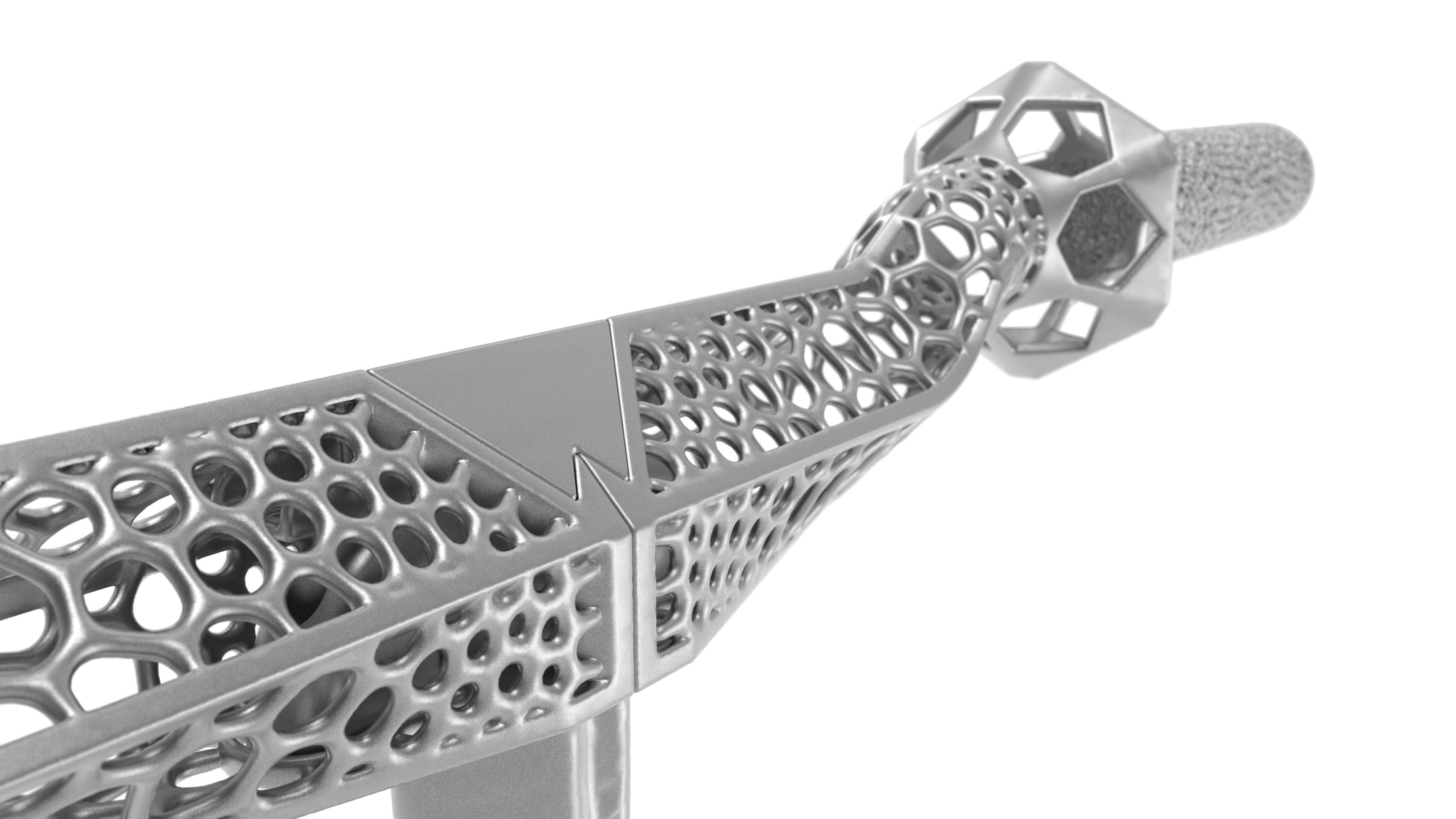
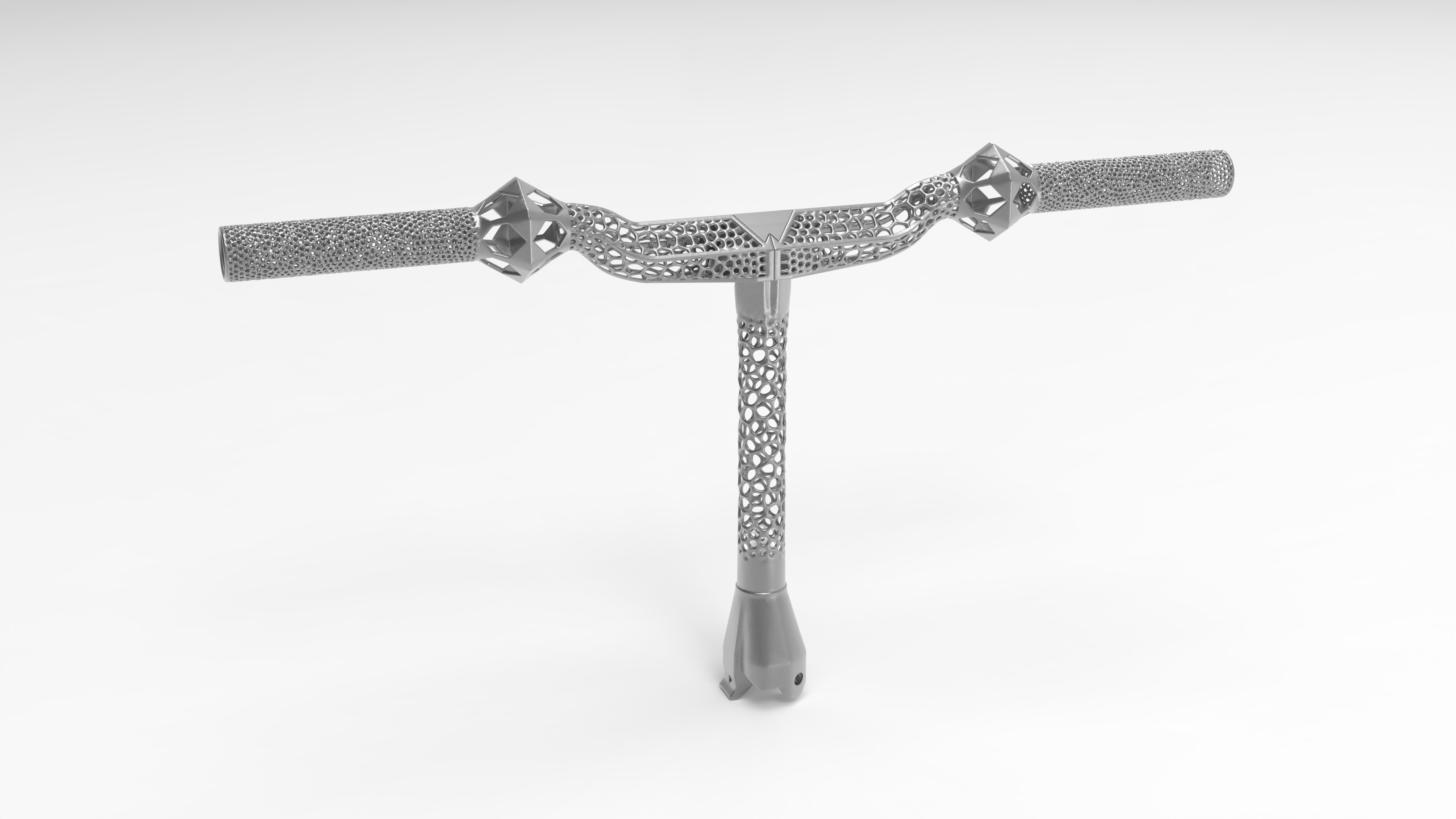

Rendering of parts and their hole structures. Horizontal bar with varying hole sizes (left), whole concept together (middle), and a close-up of rough surface on the handlebar (right).
To test user interaction, polymer prototypes were printed. The hinge was printed to enable fitting and sections of the handlebar system to assess the size, hole size, printability and to some extent the strength of the parts. Using the benefits of implicit modelling, all sharp corners were given a small fillet in nTopology to decrease residual stresses. As a next step, various mesh files were exported from nTopology so that the printability of the part could be evaluated in Materialise Magics as well as evaluating stress resistance and deformations in ANSYS.
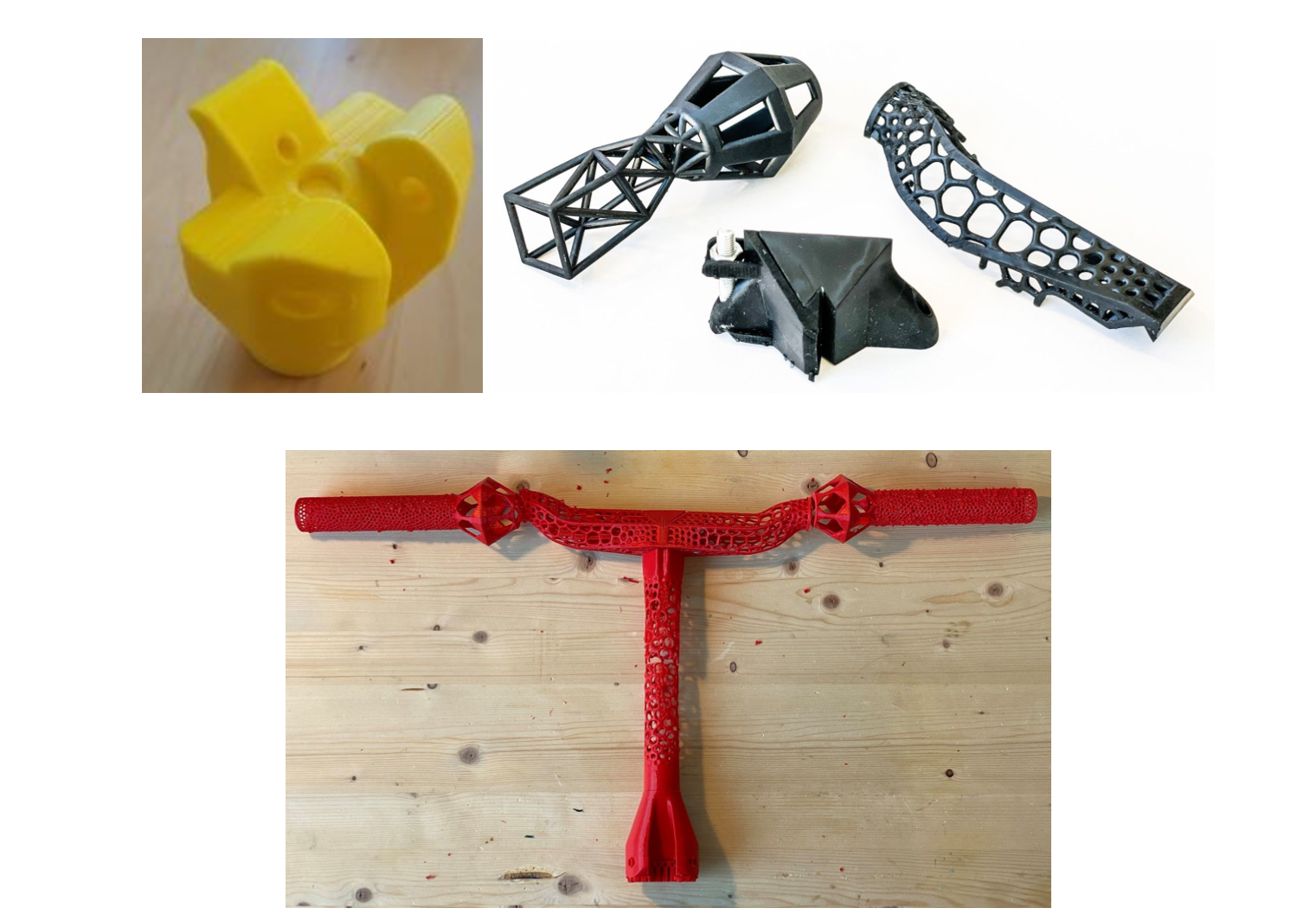
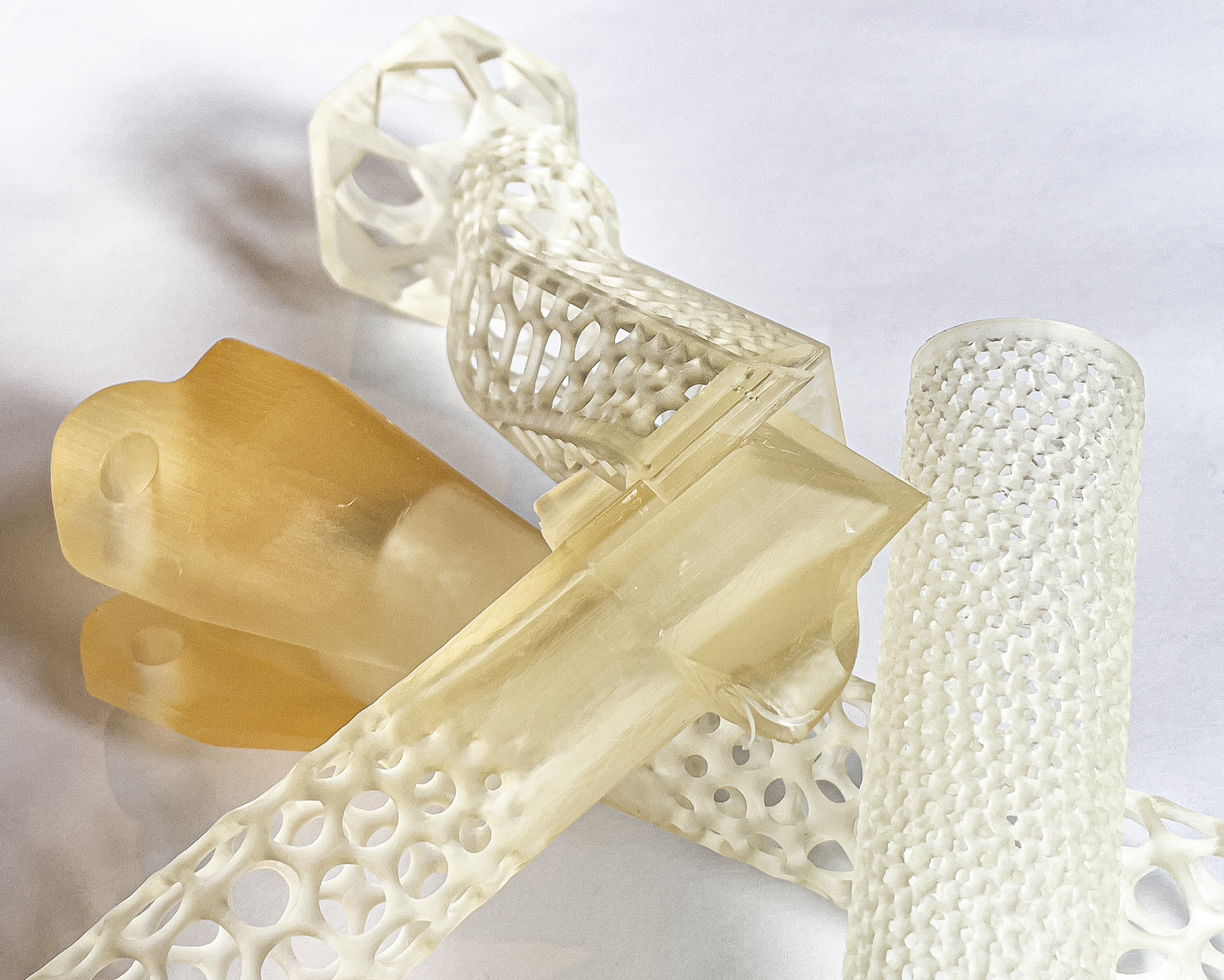
Early FDM and SLA prototypes (top left), high-resolution SLA parts to test fitting and assembly (right).
The design has three parts that will replace the steering column and handlebar of the reference design. By utilising a complex geometry the part is sufficiently strong, lightweight and has added functionality such as the possibility of internal cable management. The design is also very unique and aesthetically pleasing.
For future development brake levers, bell and gear shifter could be consolidated into the design. Additional printing of prototypes from an updated design, and further stress analysis, could create an even lighter concept and prove a feasible product for launch as an alternative to traditional handlebar systems.
Animation of assembly of the parts.